#Wissen
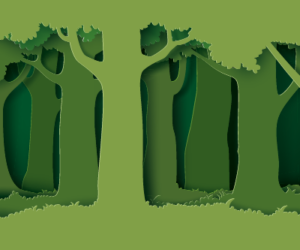
#Wissen
Text: Burkhard Maria Zimmermann
Knochenimplantate, Bauteile für Flugzeuge, ganze Häuser: Der 3D-Druck revolutioniert die Medizin, beschleunigt das Design – und hilft, die Wirtschaft nachhaltiger zu machen.
s ist wie ein Navigationssystem, nur dass man das Ziel ausdrucken und in die Hand nehmen kann. „Besonders hilfreich ist der 3D-Druck bei Fehlstellungen im Unterarm“, sagt Dr. Konrad Mader, er ist Leiter der Sektion Hand-, Unterarm- und Ellenbogentraumatologie an der Klinik für Unfallchirurgie und Orthopädie am Universitätsklinikum Hamburg-Eppendorf und Sprecher ihres Universitären Zentrums für 3D-Druck. „Wir scannen die Knochen im Computertomografen ein und drucken ein Modell aus Kunststoff, an dem wir sehen, wie wir sie korrigieren müssen.“ Die Klinik für Neuroradiologische Diagnostik und Intervention kann Aneurysmen, also Ausbuchtungen von Blutgefäßen, aus weichem Kunststoff so ausdrucken, dass die Chirurg:innen vor einer Operation testen können, wie sie einen Katheter einsetzen. Aber nicht nur bei der Planung von Eingriffen, auch beim Ersatz von Knochenmaterial kommt der 3D-Druck zum Einsatz. „Man kann schon heute Implantate aus Titan oder anderen Metalllegierungen drucken und damit Bereiche wie am Becken in ihrer natürlichen Form ersetzen, um eine Hüftprothese in einen beschädigten Knochen einzusetzen“, sagt Mader, und bei aller Professionalität ist ihm eine gewisse sachliche Begeisterung anzumerken. „Dass man passgenau so ein Implantat aus Metall herstellt, das war vor der Entwicklung des 3D-Drucks schlichtweg nicht möglich.“
Die Revolution aus dem Drucker ist in der Medizin angekommen, hat aber erst begonnen, ihr Potenzial zu entfalten. Nach einer Einschätzung des kanadischen Marktforschungsunternehmens Precedence Research, das mit Kunden wie Boston Consulting, Price Waterhouse Coopers und der Gesundheitssparte von General Electric zusammenarbeitet, sollen gedruckte Implantate im Jahr 2030 weltweit einen Umsatz von rund 8,4 Milliarden Euro erwirtschaften – 2020 lag er noch bei etwa 1,5 Milliarden Euro. Das entspräche einem jährlichen Wachstum von rund 19 Prozent, wichtigster Faktor soll dabei der Bereich der Orthopädie sein. Dabei ist der hochwertige 3D-Druck nicht zu vergleichen mit den preiswerten Geräten, die es im Elektronikmarkt zu kaufen gibt: Zu den wichtigsten Verfahren im industriellen Bereich gehört das Selektive Laser-Sintering (SLS), bei dem pulverfeine Partikel aus Kunststoff, Keramik oder Metall übereinandergeschichtet und mit einem Laser aneinandergeschweißt werden – wegen dieses „Auftürmens“ von kleinsten Teilen wird der 3D-Druck auch als Additive Fertigung bezeichnet. Die Grundlage dafür ist ein digitaler Plan des Objekts, bei der Formgebung gibt es praktisch keine Grenzen; für Krümmungen wird eine Stützstruktur mitgedruckt und anschließend entfernt. SEINE FAST ENDLOSEN ANWENDUNGSMÖGLICHKEITEN TRAGEN WOHL AUCH ZU SEINEM RASANTEN WACHSTUM BEI: Die niederländische Branchenplattform 3D Hubs stellt Teile für Toyota, Audi und die amerikanische Weltraumbehörde NASA her, und nach einer Analyse von 3D Hubs erreichte der 3DDruck im Jahr 2019 noch ein weltweites Marktvolumen von rund 11 Milliarden Euro – für 2024 liegt die Prognose bei etwa 33 Milliarden Euro. Sogar Häuser lassen sich mit einer Düse, die an einem computergesteuerten Arm hängt, Zeile für Zeile aus Beton aufsprühen: In Heidelberg, wo man bekanntlich für Zement und für Druckmaschinen ein Händchen hat, druckt die Firma Krausgruppe zurzeit das größte 3D-gedruckte Gebäude in Europa, 54 Meter lang und neun Meter hoch, die geschwungene Fassade ist in unregelmäßige Falten geworfen, wie ein weißer Vorhang vor der Zukunft. Die IT-Server, die da später einmal drinstehen, sollen es offenbar schön haben.
Mit dem verminderten Verbrauch an Kraftstoff sinken die CO2-Emissionen, und das ist nur eine Art, wie der 3D-Druck zur Nachhaltigkeit der Wirtschaft beitragen kann…
Doch die häufigsten Anwendungen finden sich bislang wohl in der industriellen Fertigung, wo Unternehmen ihre Prototypen sofort ausprobieren können, und mit größeren Anlagen stellen sie Bauteile in Mengen her, die fast an die Serienfertigung heranreichen. ABER HALTEN DIE AUCH? „3D-gedruckte Teile sind oft stabiler als gegossene oder gefräste, weil die Partikel auf Mikrometerebene miteinander verschweißt werden“, sagt Ralf Anderhofstadt, er leitet das Kompetenzzentrum für Additive Manufacturing bei Daimler Truck and Buses in Stuttgart und ist Autor des Buches „Disruptiver 3D-Druck“ 1). „Dadurch vermeidet man Unregelmäßigkeiten im Material, in denen Partikel nicht miteinander verbunden sind und die zu Bruchstellen führen können.“ Wenn’s nicht so wäre, hätte man es bei Daimler Truck schon gemerkt: Aktuell fahren etwa 60.000 3D-gedruckte Exemplare von rund 600 Bauteilen durch die Welt, darunter Griffe und Klapptische aus Kunststoff und Elemente aus Metall wie Halter für Abgasanlagen und Bauteile von Sitzen – mit der Additiven Fertigung kann das Unternehmen individuell gestaltete Teile für jeden Auftrag selbst herstellen. Noch größer als beim Fahrzeugbau sind die Vorteile des 3D-Drucks in der Luftfahrt: Wenn ein Passagierflugzeug wegen eines kaputten Teils herumsteht anstatt zu fliegen, entstehen schnell hohe Kosten; mit der neuen Technologie ist ein Ersatzteil schnell hergestellt. Außerdem lassen sich unterschiedliche Bestandteile wie Kunststoff und Kohlenstoff durch 3D-Druck zu leichten, stabilen Materialien verbinden, und das Verfahren ermöglicht Bauteile mit Hohlräumen, die ebenfalls das Gewicht der Maschine reduzieren. Der IT-Branchenverband Bitkom hat ausgerechnet, dass jedes eingesparte Kilo während der Lebensdauer des Flugzeugs durch geringeren Treibstoffverbrauch mehrere Tausend Euro einspart, eine Airline erreicht in der Summe schnell Dimensionen von mehreren Milliarden Euro – kein Wunder also, dass sich heute in einem Airbus A350 rund 1.000 Teile aus dem 3D-Drucker befinden.
Mit dem verminderten Verbrauch an Kraftstoff sinken die CO2-Emissionen, und das ist nur eine Art, wie der 3D-Druck zur Nachhaltigkeit der Wirtschaft beitragen kann: In einem Lager stecken Ressourcen wie Stahl und Beton und es muss beleuchtet und beheizt werden; bei der Fertigung nach Bedarf ist eine Lagerung auf Vorrat kaum noch nötig. Häufig werden konventionell hergestellte Teile über Hunderte oder Tausende von Kilometern versandt, auch diese Umweltbelastung entfällt. Und: „Es wird viel weniger Material eingesetzt, Reste können zerkleinert und wiederverwendet werden“, sagt Anderhofstadt. „Es bleibt zwar noch ein Schwund von zwei bis drei Prozent – beim Gießen oder Fräsen beträgt er aber bis zu 80 Prozent.“ ERKENNT DIE DEUTSCHE WIRTSCHAFT DIE STÄRKEN DES 3D-DRUCKS? „Wir waren über Jahre hinweg führend beim 3D-Druck, aber im asiatischen und amerikanischen Markt sind die Menschen häufig schneller und innovativer“, warnt Anderhofstadt. „Ich glaube, es ist im internationalen Wettbewerb wichtig, Mut zu zeigen und sich begeistern zu lassen.“ Gründe, sich zu begeistern, liefert der 3D-Druck genug. Er stellt sie ja selbst her. #
Über den Autor
Burkhard Maria Zimmermann
Burkhard schreibt seit über 20 Jahren über alles Mögliche; hinzu kommen einige Sachen, die schwer einzuordnen sind – der Rest landet im Ordner „Vermischtes“. Eine völlig willkürliche Auswahl seiner Texte finden Sie hier: torial.com/burkhard-maria.zimmermann
In der aktuellen #printproudmagz Nr. 5 mit dem Titel „Der grüne Weg“ widmen wir uns dem wohl wichtigsten Thema überhaupt: der Nachhaltigkeit.
Wir werfen einen Blick auf vegane Druckproduktion und das große Thema Ressourcenschonung am Beispiel Papierrecycling. Außerdem beleuchten wir das wichtigste Umweltzeichen des Landes, den Blauen Engel. Und erfahren Sie, warum der deutsche Thriller-Starautor Sebastian Fitzek im Interview mit #printproudmagz zugibt, ein Weichei zu sein.
Lesen Sie jetzt:
Bist auch du #printproud wie wir?
Benötigst Unterstützung bei der Konzeption, Umsetzung, Produktion oder Vermarktung deines Printprodukts?
Oder möchtest dein Projekt hier vorstellen?
Dann sollten wir unbedingt sprechen:
Tel. 040/23 51 92 15 oder kontakt@msbruno.de